Dust Collector Explosion Protection
Dust collectors may be protected with “passive” or “active” systems depending on several factors such as the location of the equipment, the dust explosion characteristics, lower total cost of ownership, and more. Passive explosion protection systems react to a deflagration’s pressure, while active explosion protection includes electronic detection and control which activates connected systems within milliseconds of detection.
How Does It Work?
Fire Suppression
Without effective dust collector fire protection systems, deep-seated dust collector fires can be a risk to the entire production plant.
Fike's offers fire suppression systems for dust collectors, designed to meet NFPA 652 (Chapter 9) compliance and ensure the detection and extinguishment of dust collector fires.
- Offered in both Carbon Dioxide (for applications without metal dust) and IG-01 Argon (for applications with metal dust).
- Includes all required components: suppression bottles, SHP-Pro releasing fire control panel, heat detectors, discharge nozzles, manifold system, siren, stop valve, enclosure and more.
- Up to 7-minute system discharge time.
- Up to 20-minute agent hold time within the dust collection equipment.
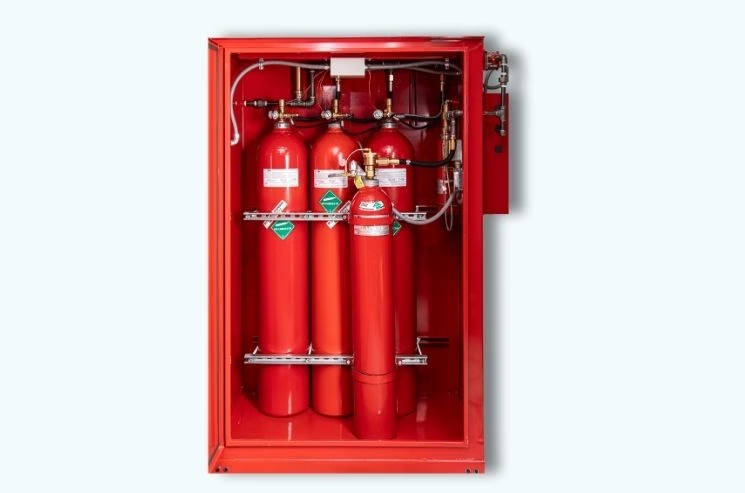
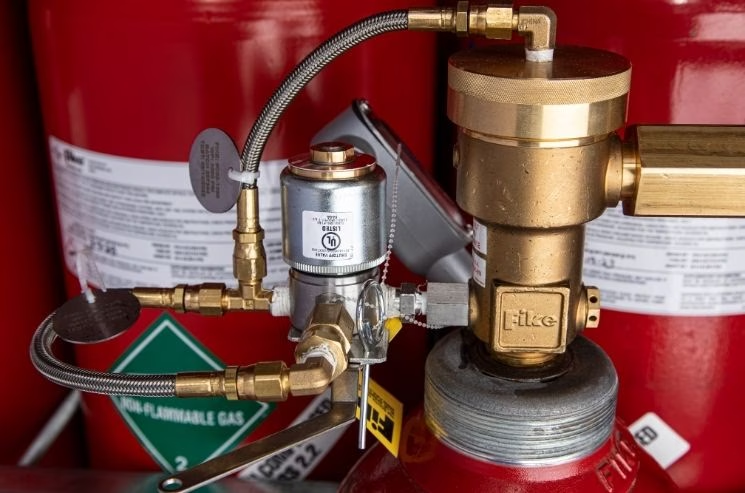
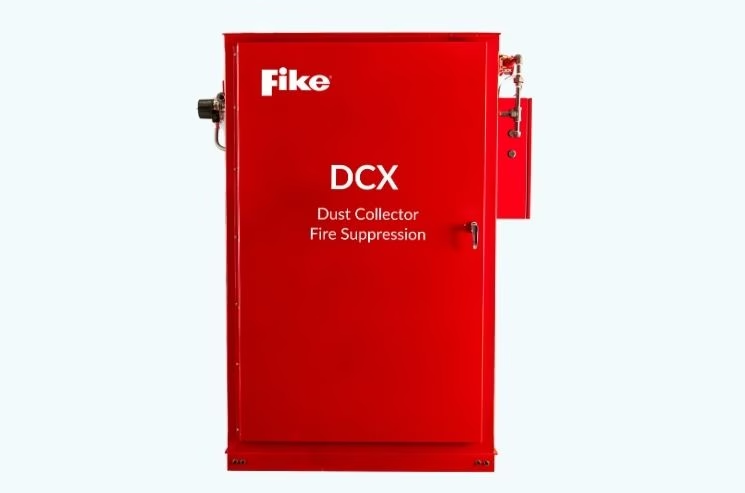
Test Protection On Your Dust Collector
This easy-to-use tool helps confirm which protection methods are available for your equipment based on its handled dust type, size, location and more. Results and recommendations are then emailed to you for your records.
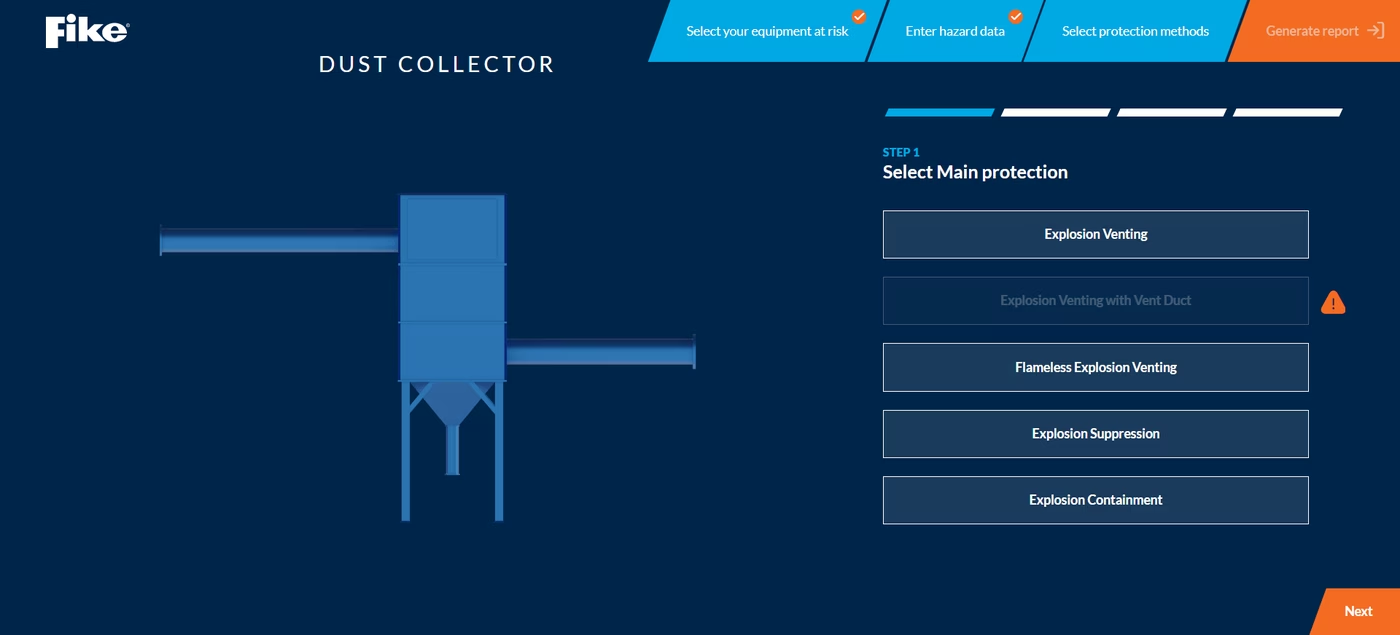
Dust Hazards & Ignition Risks
Air filled with dust particles enters the dust collector through the dirty air plenum (DAP). As the air exits the dust collector through the clean air plenum (CAP), the dust is filtered and dropped into the hopper.
The greatest explosion risk is usually found in the hopper, where the greatest open volume exists, and therefore where the largest dust cloud may occur.
If one of the following ignition sources are present, the dust may ignite and could result in a devastating explosion:
- Electrostatic discharge from non-conductive or badly bonded filter bags.
- Sparks and embers pulled into the dust collector from upstream processes such as dryers and mills.
- Smoldering of accumulated product in the hopper of the dust collector.
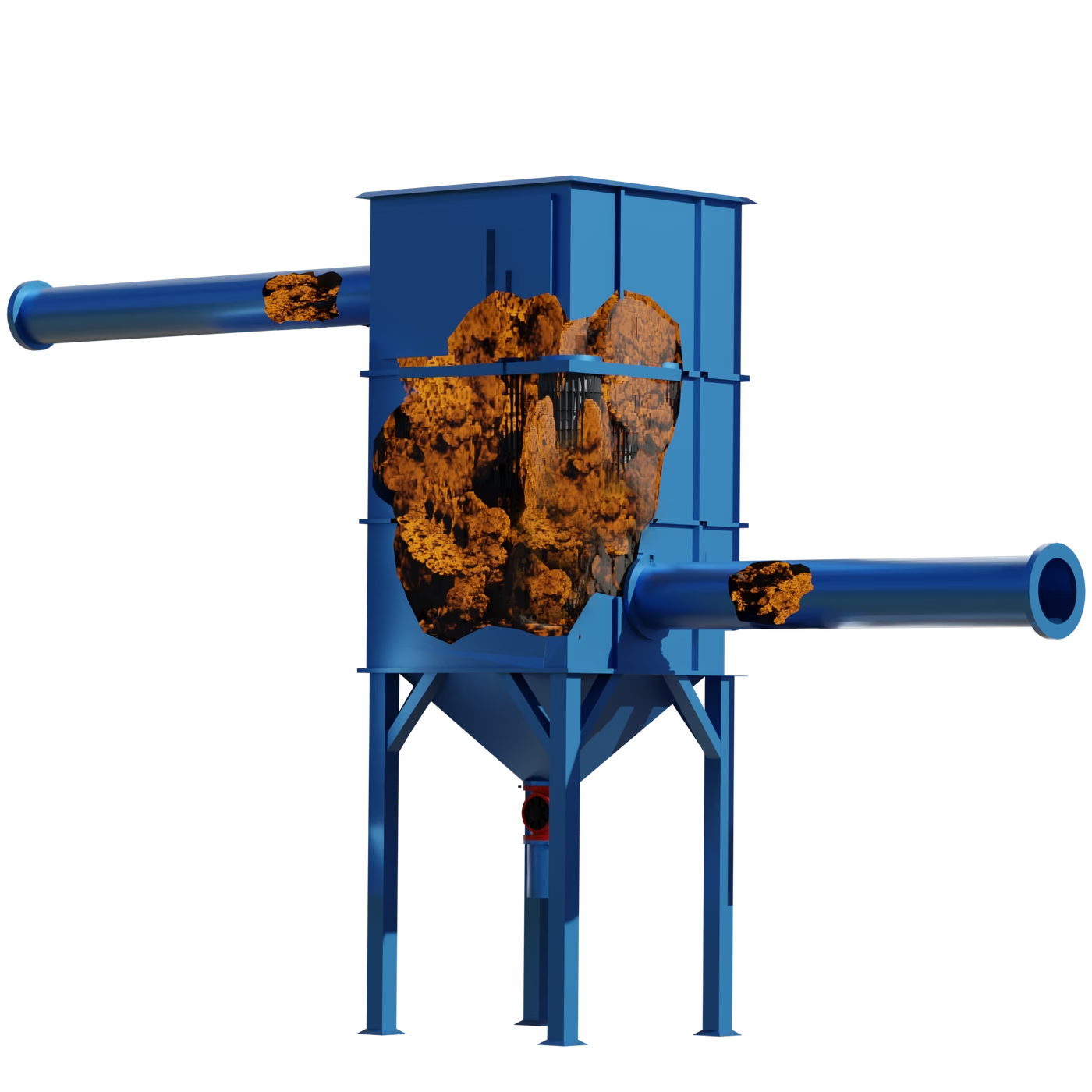
The Solutions
Due to dust collectors’ fine dust particles, interconnectivity to other equipment of the process, and prevalence of dust accumulation and dust clouds, explosion prevention and good housekeeping efforts may be employed to reduce the ignition risk. Some of these preventative methods may include:
- Antistatic bag material.
- Electrical bonding and grounding of filter bags.
- Automated ground continuity supervision.
- Spark or ember detection on dusty air inlet and spark suppression or isolation.
- Temperature supervision.
- Carbon monoxide monitoring.
However, because of the aforementioned hazards specific to dust collectors, explosion mitigation devices often must be installed to ensure the protection of workers, equipment and business continuity, as well as to comply with NFPA standards.
Explosion protection methods may include an active system, which uses sensors to detect explosion pressure waves, flames or sparks, and then relays a signal to activate a device such as a suppression bottle or an explosion isolation valve; or a passive system, which uses vents and explosion valves that activate from the pressure wave itself.
While passive solutions are more cost effective to install and maintain, active systems minimize the damage and loss once an explosion occurs and may allow for faster post-event startup.
Regardless of the type of system, any explosion protection strategy must include devices to protect both the dust collector from the initial deflagration as well as downstream and upstream equipment from secondary explosions.
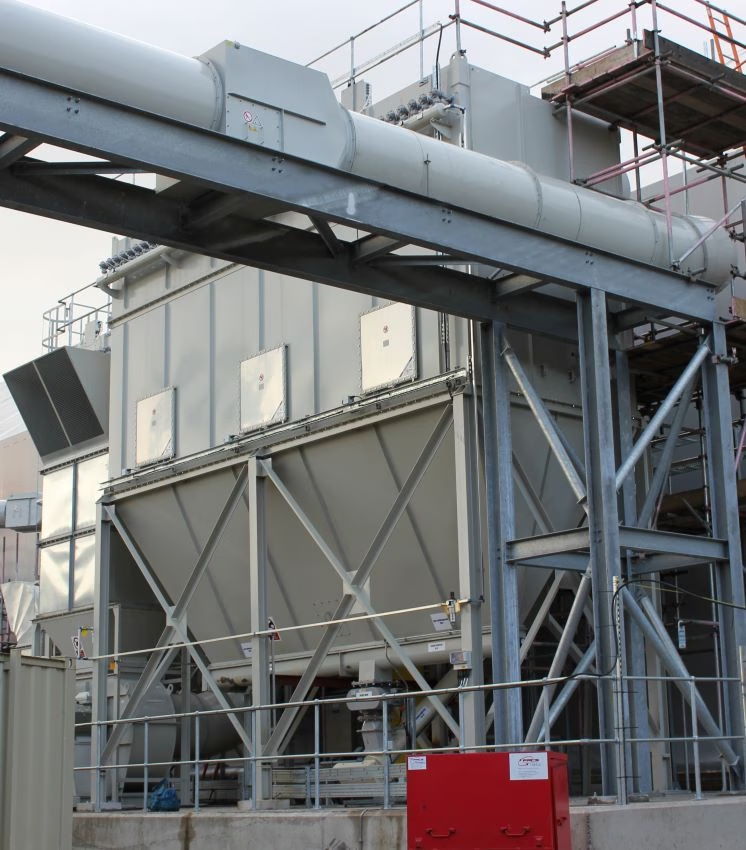
1. Protecting the Vessel: Explosion Venting
Explosion vent panels are one of the most economic and convenient solutions to prevent explosions from reaching their potential maximum pressures.
When a deflagration occurs, vent panels serve as the weak point of the enclosure and provide a pathway for expanding pressures and flames to escape. On dust collectors, explosion vent panels are usually installed on the enclosure in the area with the highest potential deflagration origination (often on the side of the dirty air plenum, and close to the hopper), with the lowest flow restrictions to the vent opening.
Explosion venting is relatively inexpensive compared to other protection methods and requires little maintenance, but a large external exclusion zone must be available and post-explosion fires may take place inside the protected vessel.
If the dust collector is installed indoors, a vent duct between the explosion vent panel and outside building wall may be used to vent the explosion out of the building. Otherwise, a flameless venting device may be placed on top of the explosion vent panel. The flameless venting device contains a flame filter that extinguishes the explosion flames and additionally a fine particle retention screen which prevents most unburnt fuel particles from being discharged, preventing secondary explosions outside the vessel.
Flameless venting is often used when:
- Equipment is indoors.
- Release of dust and flame outdoors through a vent duct is not possible.
- Personnel may be within proximity of the vent panel.
- Secondary explosion risks outside the vessel are present.
When applying explosion venting, venting parameters such as blockage by bag filters, efficiency impact of vent ducts and more must be taken into account. These are just a couple of factors that are considered by the Fike applications team during venting system design process.
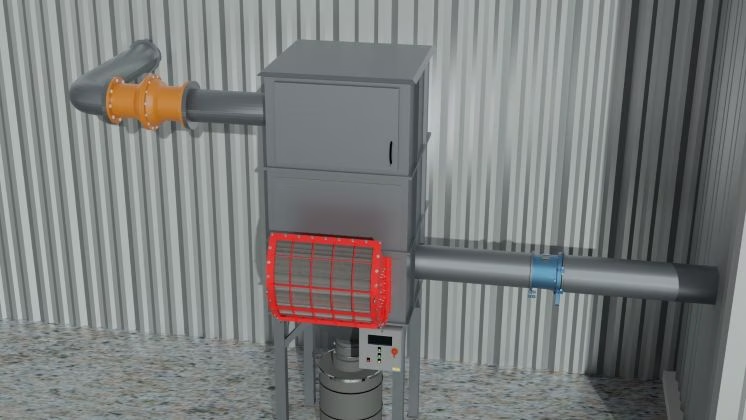
2. Protecting the Vessel: Explosion Suppression
Explosion suppression systems extinguish explosions at an early stage preventing the pressure rising above the equipment strength. A control panel continuously monitors explosion pressure detectors which will detect an explosion in its incipient stage. When detected Fike HRD bottles will inject suppressant powder into the dust collector to suppress the deflagration. These systems protect without pressure and flame discharge from the protected vessel and secondary fire and explosion risks are very low.
Suppression systems may be recommended or required in favor of venting solutions for the following reasons:
- Reduces the pressure of deflagration to protect enclosure integrity.
- Extinguishes the flame within the dust collector, reducing fire damage potential.
- Eliminates the flame release and eliminates the pressure path associated with explosion venting.
- Eliminates the discharge of toxic or hazardous materials outside of the dust collector enclosure.
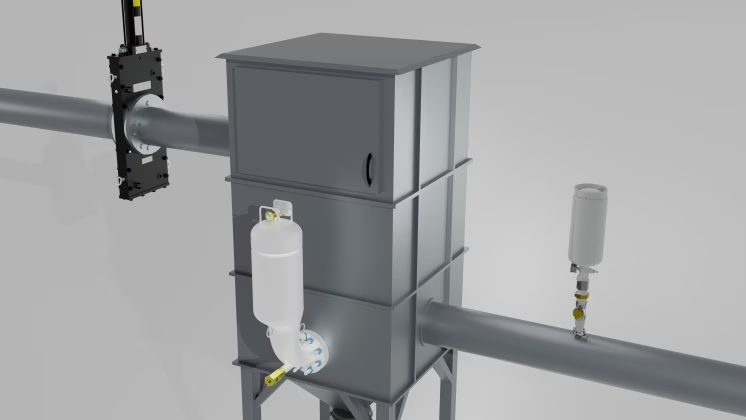
3. Protecting Connected Equipment: Isolation
Stopping an explosion from spreading upstream and downstream into connected pipes and equipment is as important as containing the initial deflagration itself.
If flame is allowed to propagate to interconnected vessels, it can lead to pressure piling, where the pressure is built up in the adjoining vessel prior to the flame arriving. The ensuing deflagration in this connected vessel then starts at an increased pressure with correspondingly more serious consequences, both in terms of the rate of combustion and final pressure.
And because many of the explosive events per year originate from dust collectors, isolating these enclosures from the rest of the process is essential to maintaining a safe process.
The dusty air inlet is the most hazardous of the connected ducts due to the amount of combustible material present. If venting is used to protect the vessel, Fike’s Dual-Flap Isolation Valve (DFI) is often used; if suppression is used to protect the vessel, chemical barriers are often chosen to isolate the dusty air inlet.
If guaranteed that there is no flame propagation risk in the clean air outlet, e.g. in case of filter cartridges certified to isolate the explosion flame, or flame release through the clean air outlet into a safe area, no additional protection measures are required. However if protection is required a passive isolation valve such as the VENTEX will not only isolate explosion flames but also protect equipment such as the process fans against the explosion pressure wave.
Lastly, the collection bin/hopper may not require protection if the rotary valve between the discharge receiver and dust collector is third-party approved as an isolation device. A non-certified rotary valve may be used when a sufficient product level in the hopper can be guaranteed at all times to effectively act as a product stop during and explosion. If the rotary valve isn’t capable of explosion isolation, a chemical barrier or active mechanical isolation valve would be needed.
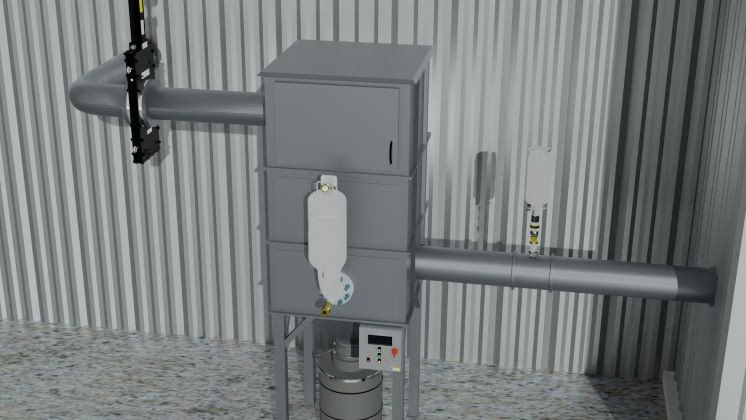