Explosion Hazard Consultancy
If you need help identifying the dust hazards in your industrial process or complying with your local standards, Fike offers unmatched explosion protection consulting for your unique process.
Solving Your Combustible Dust Problems
Do you have a combustible dust problem and are unsure of what to do next? Fike’s Explosion Safety Consultants are ready to answer any of your questions or help develop your Action Plan, which begins with a simple conversation. Our capabilities include but are not limited to the following:
A review of your process documentation or a facility walkthrough to identify where combustible dust hazards may exist and to determine whether the conditions to initiate an explosion or fire are present.
An NFPA or ATEX-required risk assessment which documents the potential consequences of a fire or explosion, determines if existing safeguards would reliably protect against a deflagration, and offers additional suggestions to reduce risk based on severity of the hazard.
Learn MoreCombustible fuel characteristics are necessary to understand if your facility is at risk and used in the design of protection systems. Fike’s on-site combustion test lab identifies Pmax, Kst, MIE, MIT and other explosibility values of the dust handled or stored in your facility.
Dust TestingUsed to accurately simulate the propagation of pressure and flames within your process to design and allow optimization of the explosion protection concept for your facility's unique dust, process and equipment.
Determines the explosion pressure resistance of your process equipment which is at risk. This information is required in the system design of venting, suppression and isolation explosion protection systems.
Strategizes risk-reduction actions and investments to make that aligns with your budgetary, production and logistical requirements.
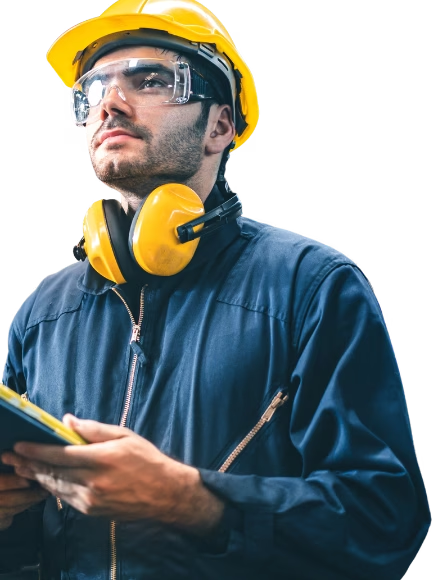
Meet The Fike Consultancy Experts
Our consultants have combined experiences exceeding 80 years of field combustion hazard consulting. They offer objective insight into what hazards exist in your facility, how to address each hazard in both priority and efficiency.
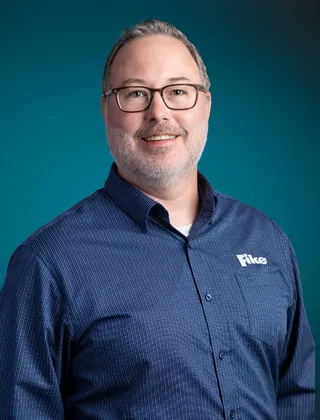
Brian Edwards, PE
- Licensed civil and environmental engineer.
- 20 years experience in safety and environmental consulting.
- Member of NFPA Industrial Fire Protection Section, and past experience sitting on NFPA 61 and 664.
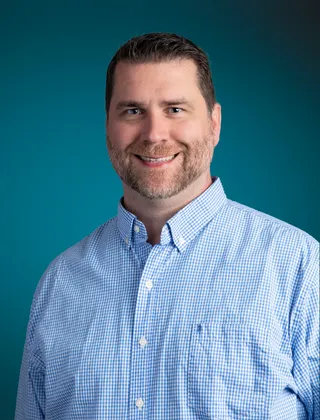
Jeff Davis, PE
- Licensed professional engineer.
- 15 years of consulting with a focus on combustible dust, gases and liquids, and OSHA's PSM and EPA's RMP standards.
- Member of NFPA; previously a principal member on NFPA 61, 91, 654, 655, and 664.
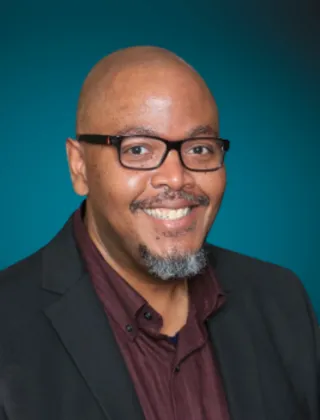
Kevin Jeffries, CFEI, CFPS, CEAS
- B.S. Occupational Safety & Health from North Caroline A&T State University
- 28 years of experience in fire prevention, protection, and code compliance.
- Certified Fire and Explosion Investigator (CFEI), Certified Fire Protection Specialist (CFPS), and Certified Ergonomics Assessment Specialist (CEAS)
- Current member of NFPA, ASSP, SFPE, NAFI and IAFI.
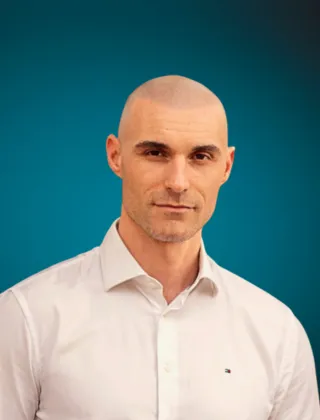
Javier Martín
- B.S. in Chemical Engineering and is currently a Ph.D. candidate in Engineering, specializing in Risk Analysis.
- 16 years of experience as an Explosion Protection Designer and Applications Specialist
- He is a member of the European Committee for Standardization CEN/TC305/WG 2.

Dilip Arulappan, MSc
- MSc process safety and loss prevention engineering
- More than 10 years of engineering and process safety consulting experience
- Member of IChemE Process Safety and an Exida certified Functional Safety Professional
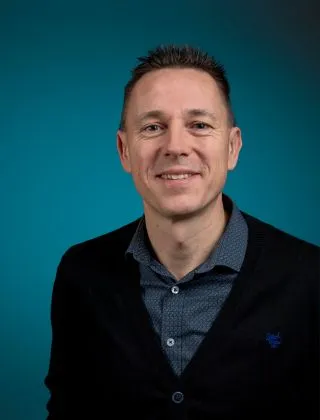
Jim Vingerhoets, MSc
- Civil Engineer
- More than 15 years of experience in explosion safety, risk assessments, consequence modelling, protection technology and design, engineering and innovation
- Delegate in European Standardization Committee CEN/TC305
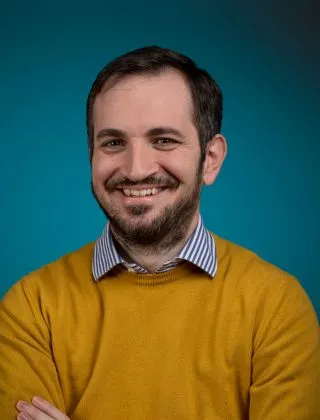
Dimitrios Kakogiannis, PhD
- Mechanical and Aeronautical Engineer
- 16 years of experience in R&D of emerging technologies for military and industrial applications in the domain of explosion protection
- Currently active working member of. European Standardization Committee CEN TC 305 WG3
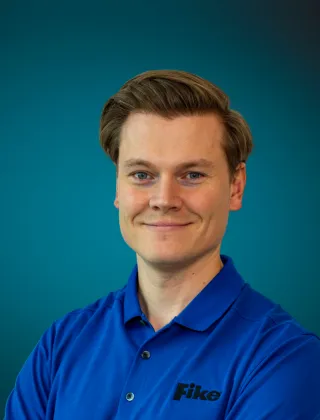
Luc Cormier, P.Eng.
- 12 years of experience in fire protection engineering and consulting. His areas of expertise include dust hazard analyses and hazardous area classification focusing on industrial explosion and process safety engineering.
- He is a member of the Society of Fire Protection Engineers and has received formal training (IECEx) in performing hazardous area classification studies.
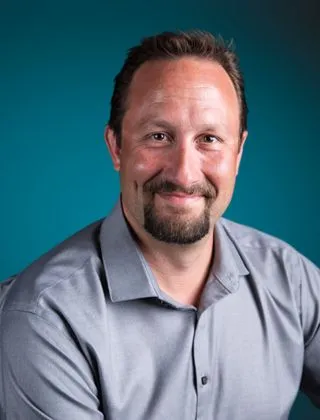
Tom Farrell
- M.S. Aerospace Engineering
- Certified LabVIEW Associate Developer (CLAD)
- More than 20 years of experience researching, developing and testing industrial processes, where risks exist, and how to prevent and protect the people and assets working on or in those processes.
Hazard Identification
This process not only identifies where hazards exist but also where hazards don’t exist, so the focus can remain on the most dangerous areas. We will review process flow diagrams of your facility’s process, particularly areas which:
- Handle dust in a way that may create a dust cloud.
- May introduce an ignition source into the process.
- Have various “states” of operation and variables to consider.
Once the hazardous areas have been identified, we will then determine how an explosion or fire could occur within those zones by determining the following:
- How is the material within the equipment being handled and conveyed?
- What are the explosibility characteristics of the material?
- Is there enough room to create a dust cloud?
- Could the equipment create or support conditions for an explosion or fire?
- Do solid materials exist which may not have the potential to explode but could catch fire?
Finally, we will identify possible ignition sources within each of the hazardous zones. Common ignition sources include: open flames or heat from welding, hot surfaces from combustion equipment, frictional heat from overheated bearings or other malfunctioning equipment, electrostatic discharges from non-grounded equipment, and many more.
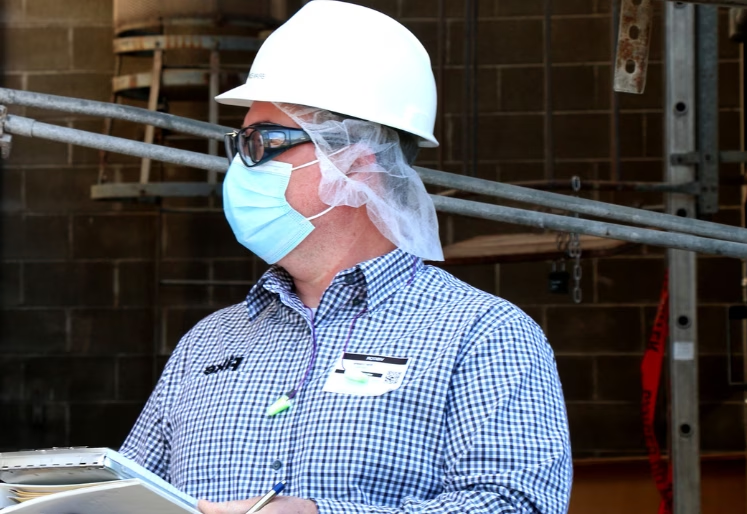
Dust Testing
Knowing the explosibility properties of your dust is necessary to determine the potentially hazardous areas within your facility and will also be used to assist with any future explosion and fire protection system design processes. Furthermore, having this information documented is required by NFPA 652.
Several resources exist to identify explosibility values such as Pmax, Kst and minimum ignition energy (MIE) for various agricultural dusts, chemical dusts, plastic dusts and metal dusts. Additionally, Fike’s Combustion Test Lab may be used to perform dust testing when:
- The dust is non-traditional and little information about the dust’s explosibility has been documented.
- The process handles a mixture of various dusts, creating a unique composition.
- Specific combustibility values are needed for explosion protection system design efforts.
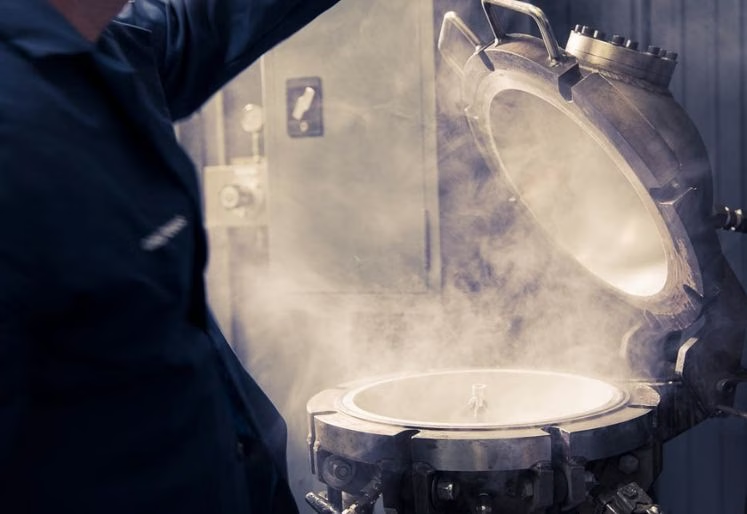
Documenting the explosibility of your facility’s dust is as simple as…

Contact
Fike’s Combustion Test Lab and tell us about your objectives for the testing.

Collect & Ship
a sample of your facility’s dust to the Combustion Test Lab.

Receive
a report that details your dust’s explosive properties in as few as two weeks.
Computational Fluid Dynamics
Computational Fluid Dynamics (CFD) uses numerical analysis and data structures to simulate the flow of fluid and gases within various fields of study including aerodynamics and weather simulations. Fike is one of the only explosion protection partners with access to this technology, and the experience to effectively use it, to accurately simulate the propagation of pressure and flames within your process.
CFD may be used to design and allow optimization of the explosion protection concept for your facility's unique dust, process and equipment. Scenarios in which CFD may be used to visualize combustion and include:
- Gas explosion applications.
- Interconnected equipment and large, long conveyors.
- Non-standard process conditions.
- Recreation of pressure and flame effects in and outside the protected equipment.
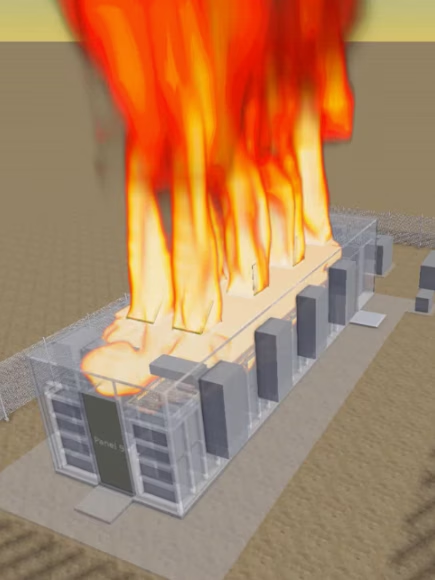
Vessel Strength Analysis
Calculating the explosion pressure resistance of any of your at-risk equipment is important for a variety of reasons. For example, in some situations, vessel strength analysis may determine that your vessel is strong enough to withstand the initial deflagration from its handled dust, and only explosion isolation devices are needed to ensure the explosion doesn’t propagate into connected equipment.
However, more commonly, the data from vessel strength analysis is required to determine a number of important factors in the design of your explosion protection system, including venting, suppression and isolation solutions:
- Quantity of devices.
- Installation location of devices.
- External flame and pressure effects.
- Recoil forces on processing equipment.
- Total reduced pressure.
- And much more.
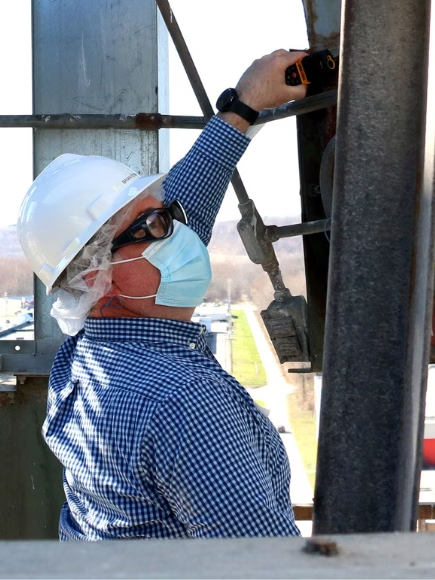
Protection Strategy Development
Not only can you trust Fike with ensuring the safety of your workers and facility but also meeting your business needs.
That’s why when necessary we work with our customers to develop a “Phased Explosion Protection Strategy,” a plan set over several weeks, months or years to work toward full protection and regulatory compliance.
The benefits of a Phased Explosion Protection Strategy include:
- Prioritize Hazard Areas
-
Identify and protect the most critical areas and equipment of your facility. Having a plan that works toward full protection often satisfies AHJ’s requirements and other regulations.
- Meet Budgetary Needs
-
Allows you to prepare budgets over the course of several months or years in preparation of reaching full safety and compliance within one or multiple facilities.
- Minimize Downtime
-
Installing and commissioning explosion protection systems requires temporary system shutdown. Our team can work with you to plan out these logistical concerns in advance to maximize business continuity.